December 6, 2024
~:
5 Mins
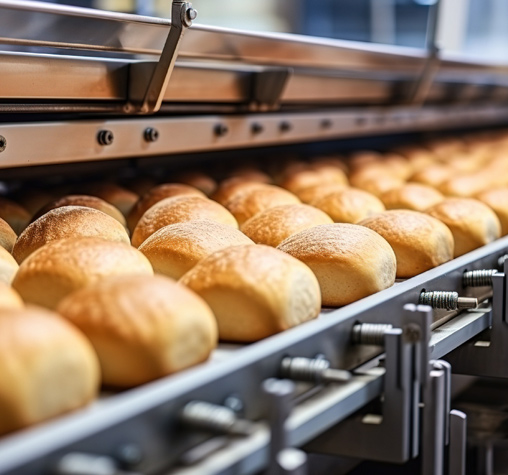
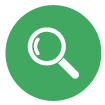
A manufacturer in the baking industry needed an innovative solution for their clean-in-place (CIP) process to improve sanitation efficiency. Prior to project engagement, adjustments to the CIP process required an automation or controls engineer to access the PLC code, which was both time-consuming and costly. The manufacturer sought a user-friendly system that would allow process experts, without programming expertise, to adjust the CIP skid without external engineering support or PLC programming. This was critical to ensure rapid response times for sanitation changes while maintaining food safety standards.
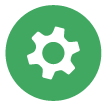
The Challenge
This project posed several challenges. First, the design had to be flexible enough to accommodate a wide range of CIP applications. The system also needed to support different VFD sizes and I/O spacing configurations, while remaining compact enough to fit on the CIP skid. Additionally, the team had to devise a method to automate the creation of L5X files from an Excel-based pin chart and import these changes into the PLC seamlessly, without an automation engineer. Furthermore, a reporting system was required to track and generate CIP data, and the team had to navigate security concerns regarding who could access and modify the settings (for example, sanitation personnel needed to change settings but not operators).
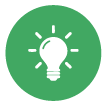
The Solution
The team delivered a standalone system that provided all the automation and controls necessary for the CIP skid. This included:
- A VFD for a 20 HP motor
- Temperature and pressure sensors wired to Flex I/O
- An opacity meter
- A 4-slot chassis for the onboard PLC, including a high-speed counter card and network cards
- A thin client display capable of running both AB FT SE and Microsoft Excel
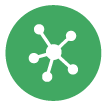
The Impact
The solution was successfully implemented across multiple sites, and the customer was highly satisfied. The ability to make quick process adjustments without needing an engineer significantly reduced both downtime and maintenance costs. The system’s flexibility allows it to be easily integrated across different plants, requiring only a 480V power connection and network cables for installation. The system was designed with straightforward disconnects for easy maintenance, further simplifying operations. User security was implemented, ensuring that only authorized personnel (such as sanitation teams) could adjust the system, while operators were restricted from modifying settings.
Relevant Case Studies
Clear Filters
INSIGHTS
Distributed HMI Systems and Remote Automation for Efficient, Safe Manufacturing
INSIGHTS
Leveraging Intrinsically Safe I/O Systems to Ensure Plant Safety
INSIGHTS
Minimizing Downtime While Ensuring Worker Protection in Hazardous Environments