December 6, 2024
~:
5 Mins
Real-Time Recipe Management
Automated Recipe Updates and Ingredient Tracking Across Continents
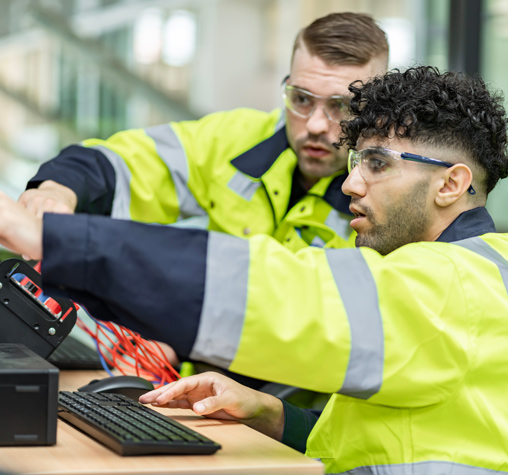
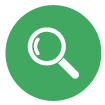
A global beverage maker with a concentrate facility in Europe needed a robust recipe management system to streamline production and support real-time recipe updates from their corporate division in North America. The company sought to create a system where the North American labs could push new recipes directly to the European plant, automating the process and minimizing manual input from operators. This initiative was essential to expand their European footprint and develop a scalable model to accommodate projected growth.
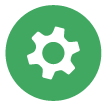
The Challenge
This project presented multiple challenges, the most significant being the need to develop and install the system entirely from the United States without any team members physically present on site due to the global COVID-19 pandemic. Additionally, the project team needed to ensure seamless communication and transmission of data between the plant’s new Ignition SCADA system and the MES Sepasoft module. This was crucial for tracking available ingredients and maintaining timely data synchronization between North America and Europe. The customer had never implemented such a system before, so gaining full buy-in and cooperation from their team required ongoing communication and collaboration.
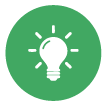
The Solution
The team implemented a new Ignition® SCADA system to manage all controls, data, and reporting within the plant. This system was linked to a secondary Ignition server running an MES Sepasoft module, which specialized in material traceability and recipe management in the process line. This design allowed the North American labs to push new recipes to the European plant in real time. With the system, the customer could automatically track the ingredients available in the European facility, allowing operators to select the recipe and start production immediately. By maintaining real-time data transmission, the solution ensured data accuracy and synchronization between the plant and corporate headquarters. This seamless flow of data enabled faster, more accurate decision-making across both locations.
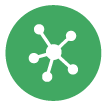
The Impact
Despite the complexity and remote nature of the project, the system operated as expected from the first deployment, with a 97% recipe tolerance achieved by the second test batch. The customer was highly satisfied with the ability to monitor and update recipes in real time, enabling more efficient production and future scalability. The success of this project set the stage for potential retrofitting of existing plants and expansion to future facilities.
Relevant Case Studies
Clear Filters
INSIGHTS
Distributed HMI Systems and Remote Automation for Efficient, Safe Manufacturing
INSIGHTS
Leveraging Intrinsically Safe I/O Systems to Ensure Plant Safety
INSIGHTS
Minimizing Downtime While Ensuring Worker Protection in Hazardous Environments